Volume : V, Issue : V, June - 2015 "THE EVALUATION OF 5'S SYSTEM" WITH REFERENCE TO ABHIJAT EQUIPMENTS PVT. LTD., SATARA”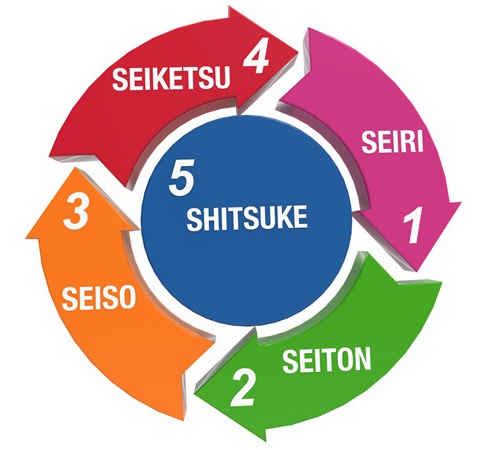 Santosh Chavan, Sarika Bhosale By : Laxmi Book Publication Abstract : The theory behind the 5S concept is to basically manage the work space in an organised way. As with the lean thinking concept, which is intertwined with this business theory, the whole aim is to look at the work flow, improve all the inefficiencies within it, remove all the waste and by keeping the whole working environment neat and tidy then a safe working space is maintained. Thus employees feel that the areas in which they spend all of their working days are clean, tidy and good to work in. It’s a way of improving business whilst taking into account the environmental needs of the staff. In working environment employees try to keep the working areas clean and bright. In business operations management and staff are encouraged to come up with ideas on how we can improve our work by being a slick organisation. Business has a tendency to put up barriers especially those that will slow a process down. The job is to challenge those barriers and move forward as quickly as possible. Keywords : Article : Cite This Article : Santosh Chavan, Sarika Bhosale(2015). "THE EVALUATION OF 5'S SYSTEM" WITH REFERENCE TO ABHIJAT EQUIPMENTS PVT. LTD., SATARA”. Indian Streams Research Journal, Vol. V, Issue. V, http://isrj.org/UploadedData/6723.pdf References : - K. Ganapathy, Prof. V. Narayana, B. Subramanian – FIVE S, Quality Circle, Forum of India, Secunderabad.
- Motwani, J. (2003). A business process change framework for examining lean manufacturing: a case study. Industrial Management & Data Systems , 339-346.
- Shah, R. (2003). Lean manufacturing: context, practice bundles, and performance. Journal of Operations Management , 129-149.
- Ardith Ct., B. C. (2005). Workplace Color Coding Standards. visualworkplace , 1-5.
- Bayo‐Moriones, A. (2010). 5S use in manufacturing plants: contextual factors and impact on operating performance. International Journal of Quality & Reliability Management , 217 - 230.
- B. Modarressa, A. A. (2007). Kaizen costing for lean manufacturing: a case study. International Journal of Production Research , 1751-1760.
- LISTA. (2012, november 5th). A three-step process for improving efficiency and productivity. Implementing 5S Workplace Organization , pp. 1-5.
- Bresko, M. (2005). The 5S Method of Improvement - Enhancing Safety, Productivity and Culture. ReliabilityDirect , 1-3.
- Ardith Ct., B. C. (2005). Workplace Color Coding Standards. visualworkplace , 1-5.
- Bayo‐Moriones, A. (2010). 5S use in manufacturing plants: contextual factors and impact on operating performance. International Journal of Quality & Reliability Management , 217 - 230.
- K. Ganapathy, Prof. V. Narayana, B. Subramanian – FIVE S, Quality Circle, Forum of India, Secunderabad.
- Motwani, J. (2003). A business process change framework for examining lean manufacturing: a case study. Industrial Management & Data Systems , 339-346.
- Worley, J. (2006). The role of communication and management support in a lean manufacturing implementation. Management Decision-Journal of Management History merged into Management Decision , 228-245.
- Shah, R. (2003). Lean manufacturing: context, practice bundles, and performance. Journal of Operations Management , 129-149.
- B. Modarressa, A. A. (2007). Kaizen costing for lean manufacturing: a case study. International Journal of Production Research , 1751-1760.
- LISTA. (2012, november 5th). A three-step process for improving efficiency and productivity. Implementing 5S Workplace Organization , pp. 1-5.
- Bresko, M. (2005). The 5S Method of Improvement - Enhancing Safety, Productivity and Culture. ReliabilityDirect , 1-3.
- Worley, J. (2006). The role of communication and management support in a lean manufacturing implementation. Management Decision-Journal of Management History merged into Management Decision , 228-245.
- B. Modarressa, A. A. (2007). Kaizen costing for lean manufacturing: a case study. International Journal of Production Research , 1751-1760.
- LISTA. (2012, november 5th). A three-step process for improving efficiency and productivity. Implementing 5S Workplace Organization , pp. 1-5.
- Ardith Ct., B. C. (2005). Workplace Color Coding Standards. visualworkplace , 1-5.
- Bayo‐Moriones, A. (2010). 5S use in manufacturing plants: contextual factors and impact on operating performance. International Journal of Quality & Reliability Management , 217 - 230.
- K. Ganapathy, Prof. V. Narayana, B. Subramanian – FIVE S, Quality Circle, Forum of India, Secunderabad.
- Motwani, J. (2003). A business process change framework for examining lean manufacturing: a case study. Industrial Management & Data Systems , 339-346.
- Bresko, M. (2005). The 5S Method of Improvement - Enhancing Safety, Productivity and Culture. ReliabilityDirect , 1-3.
- Worley, J. (2006). The role of communication and management support in a lean manufacturing implementation. Management Decision-Journal of Management History merged into Management Decision , 228-245.
- Ardith Ct., B. C. (2005). Workplace Color Coding Standards. visualworkplace , 1-5.
- Bayo‐Moriones, A. (2010). 5S use in manufacturing plants: contextual factors and impact on operating performance. International Journal of Quality & Reliability Management , 217 - 230.
- K. Ganapathy, Prof. V. Narayana, B. Subramanian – FIVE S, Quality Circle, Forum of India, Secunderabad.
- Motwani, J. (2003). A business process change framework for examining lean manufacturing: a case study. Industrial Management & Data Systems , 339-346.
- Shah, R. (2003). Lean manufacturing: context, practice bundles, and performance. Journal of Operations Management , 129-149.
- B. Modarressa, A. A. (2007). Kaizen costing for lean manufacturing: a case study. International Journal of Production Research , 1751-1760.
- LISTA. (2012, november 5th). A three-step process for improving efficiency and productivity. Implementing 5S Workplace Organization , pp. 1-5.
- Shah, R. (2003). Lean manufacturing: context, practice bundles, and performance. Journal of Operations Management , 129-149.
- Ardith Ct., B. C. (2005). Workplace Color Coding Standards. visualworkplace , 1-5.
- Bayo‐Moriones, A. (2010). 5S use in manufacturing plants: contextual factors and impact on operating performance. International Journal of Quality & Reliability Management , 217 - 230.
- K. Ganapathy, Prof. V. Narayana, B. Subramanian – FIVE S, Quality Circle, Forum of India, Secunderabad.
- Motwani, J. (2003). A business process change framework for examining lean manufacturing: a case study. Industrial Management & Data Systems , 339-346.
- Bresko, M. (2005). The 5S Method of Improvement - Enhancing Safety, Productivity and Culture. ReliabilityDirect , 1-3.
- Worley, J. (2006). The role of communication and management support in a lean manufacturing implementation. Management Decision-Journal of Management History merged into Management Decision , 228-245.
- Gapp, R. (2008). Implementing 5S within a Japanese context: an integrated management system. Journal of Management History merged into Management Decision , 565 - 579.
- Ardith Ct., B. C. (2005). Workplace Color Coding Standards. visualworkplace , 1-5.
- Bayo‐Moriones, A. (2010). 5S use in manufacturing plants: contextual factors and impact on operating performance. International Journal of Quality & Reliability Management , 217 - 230.
- K. Ganapathy, Prof. V. Narayana, B. Subramanian – FIVE S, Quality Circle, Forum of India, Secunderabad.
- Motwani, J. (2003). A business process change framework for examining lean manufacturing: a case study. Industrial Management & Data Systems , 339-346.
- LISTA. (2012, november 5th). A three-step process for improving efficiency and productivity. Implementing 5S Workplace Organization , pp. 1-5.
- Bresko, M. (2005). The 5S Method of Improvement - Enhancing Safety, Productivity and Culture. ReliabilityDirect , 1-3.
- Worley, J. (2006). The role of communication and management support in a lean manufacturing implementation. Management Decision-Journal of Management History merged into Management Decision , 228-245.
- Ardith Ct., B. C. (2005). Workplace Color Coding Standards. visualworkplace , 1-5.
- Bayo‐Moriones, A. (2010). 5S use in manufacturing plants: contextual factors and impact on operating performance. International Journal of Quality & Reliability Management , 217 - 230.
- K. Ganapathy, Prof. V. Narayana, B. Subramanian – FIVE S, Quality Circle, Forum of India, Secunderabad.
- Motwani, J. (2003). A business process change framework for examining lean manufacturing: a case study. Industrial Management & Data Systems , 339-346.
- Gapp, R. (2008). Implementing 5S within a Japanese context: an integrated management system. Journal of Management History merged into Management Decision , 565 - 579.
- Shah, R. (2003). Lean manufacturing: context, practice bundles, and performance. Journal of Operations Management , 129-149.
- B. Modarressa, A. A. (2007). Kaizen costing for lean manufacturing: a case study. International Journal of Production Research , 1751-1760.
- LISTA. (2012, november 5th). A three-step process for improving efficiency and productivity. Implementing 5S Workplace Organization , pp. 1-5.
- Bresko, M. (2005). The 5S Method of Improvement - Enhancing Safety, Productivity and Culture. ReliabilityDirect , 1-3.
- Worley, J. (2006). The role of communication and management support in a lean manufacturing implementation. Management Decision-Journal of Management History merged into Management Decision , 228-245.
- Shah, R. (2003). Lean manufacturing: context, practice bundles, and performance. Journal of Operations Management , 129-149.
- B. Modarressa, A. A. (2007). Kaizen costing for lean manufacturing: a case study. International Journal of Production Research , 1751-1760.
- LISTA. (2012, november 5th). A three-step process for improving efficiency and productivity. Implementing 5S Workplace Organization , pp. 1-5.
- Shah, R. (2003). Lean manufacturing: context, practice bundles, and performance. Journal of Operations Management , 129-149.
- B. Modarressa, A. A. (2007). Kaizen costing for lean manufacturing: a case study. International Journal of Production Research , 1751-1760.
- LISTA. (2012, november 5th). A three-step process for improving efficiency and productivity. Implementing 5S Workplace Organization , pp. 1-5.
- Ardith Ct., B. C. (2005). Workplace Color Coding Standards. visualworkplace , 1-5.
- Bayo‐Moriones, A. (2010). 5S use in manufacturing plants: contextual factors and impact on operating performance. International Journal of Quality & Reliability Management , 217 - 230.
- K. Ganapathy, Prof. V. Narayana, B. Subramanian – FIVE S, Quality Circle, Forum of India, Secunderabad.
- Motwani, J. (2003). A business process change framework for examining lean manufacturing: a case study. Industrial Management & Data Systems , 339-346.
- Ardith Ct., B. C. (2005). Workplace Color Coding Standards. visualworkplace , 1-5.
- Bayo‐Moriones, A. (2010). 5S use in manufacturing plants: contextual factors and impact on operating performance. International Journal of Quality & Reliability Management , 217 - 230.
- K. Ganapathy, Prof. V. Narayana, B. Subramanian – FIVE S, Quality Circle, Forum of India, Secunderabad.
- Motwani, J. (2003). A business process change framework for examining lean manufacturing: a case study. Industrial Management & Data Systems , 339-346.
- Shah, R. (2003). Lean manufacturing: context, practice bundles, and performance. Journal of Operations Management , 129-149.
- B. Modarressa, A. A. (2007). Kaizen costing for lean manufacturing: a case study. International Journal of Production Research , 1751-1760.
- LISTA. (2012, november 5th). A three-step process for improving efficiency and productivity. Implementing 5S Workplace Organization , pp. 1-5.
- Bresko, M. (2005). The 5S Method of Improvement - Enhancing Safety, Productivity and Culture. ReliabilityDirect , 1-3.
- Worley, J. (2006). The role of communication and management support in a lean manufacturing implementation. Management Decision-Journal of Management History merged into Management Decision , 228-245.
- B. Modarressa, A. A. (2007). Kaizen costing for lean manufacturing: a case study. International Journal of Production Research , 1751-1760.
- LISTA. (2012, november 5th). A three-step process for improving efficiency and productivity. Implementing 5S Workplace Organization , pp. 1-5.
- Ardith Ct., B. C. (2005). Workplace Color Coding Standards. visualworkplace , 1-5.
- Bayo‐Moriones, A. (2010). 5S use in manufacturing plants: contextual factors and impact on operating performance. International Journal of Quality & Reliability Management , 217 - 230.
- K. Ganapathy, Prof. V. Narayana, B. Subramanian – FIVE S, Quality Circle, Forum of India, Secunderabad.
- Motwani, J. (2003). A business process change framework for examining lean manufacturing: a case study. Industrial Management & Data Systems , 339-346.
- Ardith Ct., B. C. (2005). Workplace Color Coding Standards. visualworkplace , 1-5.
- Bayo‐Moriones, A. (2010). 5S use in manufacturing plants: contextual factors and impact on operating performance. International Journal of Quality & Reliability Management , 217 - 230.
- K. Ganapathy, Prof. V. Narayana, B. Subramanian – FIVE S, Quality Circle, Forum of India, Secunderabad.
- Motwani, J. (2003). A business process change framework for examining lean manufacturing: a case study. Industrial Management & Data Systems , 339-346.
- Bresko, M. (2005). The 5S Method of Improvement - Enhancing Safety, Productivity and Culture. ReliabilityDirect , 1-3.
- Worley, J. (2006). The role of communication and management support in a lean manufacturing implementation. Management Decision-Journal of Management History merged into Management Decision , 228-245.
- Shah, R. (2003). Lean manufacturing: context, practice bundles, and performance. Journal of Operations Management , 129-149.
- Bresko, M. (2005). The 5S Method of Improvement - Enhancing Safety, Productivity and Culture. ReliabilityDirect , 1-3.
- Worley, J. (2006). The role of communication and management support in a lean manufacturing implementation. Management Decision-Journal of Management History merged into Management Decision , 228-245.
- Ardith Ct., B. C. (2005). Workplace Color Coding Standards. visualworkplace , 1-5.
- Bayo‐Moriones, A. (2010). 5S use in manufacturing plants: contextual factors and impact on operating performance. International Journal of Quality & Reliability Management , 217 - 230.
- K. Ganapathy, Prof. V. Narayana, B. Subramanian – FIVE S, Quality Circle, Forum of India, Secunderabad.
- Motwani, J. (2003). A business process change framework for examining lean manufacturing: a case study. Industrial Management & Data Systems , 339-346.
- Shah, R. (2003). Lean manufacturing: context, practice bundles, and performance. Journal of Operations Management , 129-149.
- Gapp, R. (2008). Implementing 5S within a Japanese context: an integrated management system. Journal of Management History merged into Management Decision , 565 - 579.
- Bresko, M. (2005). The 5S Method of Improvement - Enhancing Safety, Productivity and Culture. ReliabilityDirect , 1-3.
- Worley, J. (2006). The role of communication and management support in a lean manufacturing implementation. Management Decision-Journal of Management History merged into Management Decision , 228-245.
- B. Modarressa, A. A. (2007). Kaizen costing for lean manufacturing: a case study. International Journal of Production Research , 1751-1760.
- LISTA. (2012, november 5th). A three-step process for improving efficiency and productivity. Implementing 5S Workplace Organization , pp. 1-5.
- Bresko, M. (2005). The 5S Method of Improvement - Enhancing Safety, Productivity and Culture. ReliabilityDirect , 1-3.
- Worley, J. (2006). The role of communication and management support in a lean manufacturing implementation. Management Decision-Journal of Management History merged into Management Decision , 228-245.
- Ardith Ct., B. C. (2005). Workplace Color Coding Standards. visualworkplace , 1-5.
- Bayo‐Moriones, A. (2010). 5S use in manufacturing plants: contextual factors and impact on operating performance. International Journal of Quality & Reliability Management , 217 - 230.
- K. Ganapathy, Prof. V. Narayana, B. Subramanian – FIVE S, Quality Circle, Forum of India, Secunderabad.
- Motwani, J. (2003). A business process change framework for examining lean manufacturing: a case study. Industrial Management & Data Systems , 339-346.
- Gapp, R. (2008). Implementing 5S within a Japanese context: an integrated management system. Journal of Management History merged into Management Decision , 565 - 579.
- Bresko, M. (2005). The 5S Method of Improvement - Enhancing Safety, Productivity and Culture. ReliabilityDirect , 1-3.
- Worley, J. (2006). The role of communication and management support in a lean manufacturing implementation. Management Decision-Journal of Management History merged into Management Decision , 228-245.
- Bresko, M. (2005). The 5S Method of Improvement - Enhancing Safety, Productivity and Culture. ReliabilityDirect , 1-3.
- Worley, J. (2006). The role of communication and management support in a lean manufacturing implementation. Management Decision-Journal of Management History merged into Management Decision , 228-245.
- Shah, R. (2003). Lean manufacturing: context, practice bundles, and performance. Journal of Operations Management , 129-149.
- B. Modarressa, A. A. (2007). Kaizen costing for lean manufacturing: a case study. International Journal of Production Research , 1751-1760.
- LISTA. (2012, november 5th). A three-step process for improving efficiency and productivity. Implementing 5S Workplace Organization , pp. 1-5.
- Gapp, R. (2008). Implementing 5S within a Japanese context: an integrated management system. Journal of Management History merged into Management Decision , 565 - 579.
- Shah, R. (2003). Lean manufacturing: context, practice bundles, and performance. Journal of Operations Management , 129-149.
- B. Modarressa, A. A. (2007). Kaizen costing for lean manufacturing: a case study. International Journal of Production Research , 1751-1760.
- LISTA. (2012, november 5th). A three-step process for improving efficiency and productivity. Implementing 5S Workplace Organization , pp. 1-5.
- Gapp, R. (2008). Implementing 5S within a Japanese context: an integrated management system. Journal of Management History merged into Management Decision , 565 - 579.
- Gapp, R. (2008). Implementing 5S within a Japanese context: an integrated management system. Journal of Management History merged into Management Decision , 565 - 579.
- Shah, R. (2003). Lean manufacturing: context, practice bundles, and performance. Journal of Operations Management , 129-149.
- Gapp, R. (2008). Implementing 5S within a Japanese context: an integrated management system. Journal of Management History merged into Management Decision , 565 - 579.
- B. Modarressa, A. A. (2007). Kaizen costing for lean manufacturing: a case study. International Journal of Production Research , 1751-1760.
- Ardith Ct., B. C. (2005). Workplace Color Coding Standards. visualworkplace , 1-5.
- Bayo‐Moriones, A. (2010). 5S use in manufacturing plants: contextual factors and impact on operating performance. International Journal of Quality & Reliability Management , 217 - 230.
- K. Ganapathy, Prof. V. Narayana, B. Subramanian – FIVE S, Quality Circle, Forum of India, Secunderabad.
- Motwani, J. (2003). A business process change framework for examining lean manufacturing: a case study. Industrial Management & Data Systems , 339-346.
- Shah, R. (2003). Lean manufacturing: context, practice bundles, and performance. Journal of Operations Management , 129-149.
- B. Modarressa, A. A. (2007). Kaizen costing for lean manufacturing: a case study. International Journal of Production Research , 1751-1760.
- LISTA. (2012, november 5th). A three-step process for improving efficiency and productivity. Implementing 5S Workplace Organization , pp. 1-5.
- Shah, R. (2003). Lean manufacturing: context, practice bundles, and performance. Journal of Operations Management , 129-149.
- B. Modarressa, A. A. (2007). Kaizen costing for lean manufacturing: a case study. International Journal of Production Research , 1751-1760.
- Bresko, M. (2005). The 5S Method of Improvement - Enhancing Safety, Productivity and Culture. ReliabilityDirect , 1-3.
- Worley, J. (2006). The role of communication and management support in a lean manufacturing implementation. Management Decision-Journal of Management History merged into Management Decision , 228-245.
- LISTA. (2012, november 5th). A three-step process for improving efficiency and productivity. Implementing 5S Workplace Organization , pp. 1-5.
- Bresko, M. (2005). The 5S Method of Improvement - Enhancing Safety, Productivity and Culture. ReliabilityDirect , 1-3.
- Worley, J. (2006). The role of communication and management support in a lean manufacturing implementation. Management Decision-Journal of Management History merged into Management Decision , 228-245.
- Ardith Ct., B. C. (2005). Workplace Color Coding Standards. visualworkplace , 1-5.
- Bayo‐Moriones, A. (2010). 5S use in manufacturing plants: contextual factors and impact on operating performance. International Journal of Quality & Reliability Management , 217 - 230.
- K. Ganapathy, Prof. V. Narayana, B. Subramanian – FIVE S, Quality Circle, Forum of India, Secunderabad.
- Motwani, J. (2003). A business process change framework for examining lean manufacturing: a case study. Industrial Management & Data Systems , 339-346.
- Shah, R. (2003). Lean manufacturing: context, practice bundles, and performance. Journal of Operations Management , 129-149.
- B. Modarressa, A. A. (2007). Kaizen costing for lean manufacturing: a case study. International Journal of Production Research , 1751-1760.
- LISTA. (2012, november 5th). A three-step process for improving efficiency and productivity. Implementing 5S Workplace Organization , pp. 1-5.
- Bresko, M. (2005). The 5S Method of Improvement - Enhancing Safety, Productivity and Culture. ReliabilityDirect , 1-3.
- Worley, J. (2006). The role of communication and management support in a lean manufacturing implementation. Management Decision-Journal of Management History merged into Management Decision , 228-245.
- Ardith Ct., B. C. (2005). Workplace Color Coding Standards. visualworkplace , 1-5.
- Bayo‐Moriones, A. (2010). 5S use in manufacturing plants: contextual factors and impact on operating performance. International Journal of Quality & Reliability Management , 217 - 230.
- K. Ganapathy, Prof. V. Narayana, B. Subramanian – FIVE S, Quality Circle, Forum of India, Secunderabad.
- Motwani, J. (2003). A business process change framework for examining lean manufacturing: a case study. Industrial Management & Data Systems , 339-346.
- Shah, R. (2003). Lean manufacturing: context, practice bundles, and performance. Journal of Operations Management , 129-149.
- B. Modarressa, A. A. (2007). Kaizen costing for lean manufacturing: a case study. International Journal of Production Research , 1751-1760.
- LISTA. (2012, november 5th). A three-step process for improving efficiency and productivity. Implementing 5S Workplace Organization , pp. 1-5.
- Shah, R. (2003). Lean manufacturing: context, practice bundles, and performance. Journal of Operations Management , 129-149.
- B. Modarressa, A. A. (2007). Kaizen costing for lean manufacturing: a case study. International Journal of Production Research , 1751-1760.
- LISTA. (2012, november 5th). A three-step process for improving efficiency and productivity. Implementing 5S Workplace Organization , pp. 1-5.
- Bresko, M. (2005). The 5S Method of Improvement - Enhancing Safety, Productivity and Culture. ReliabilityDirect , 1-3.
- Worley, J. (2006). The role of communication and management support in a lean manufacturing implementation. Management Decision-Journal of Management History merged into Management Decision , 228-245.
- Gapp, R. (2008). Implementing 5S within a Japanese context: an integrated management system. Journal of Management History merged into Management Decision , 565 - 579.
- B. Modarressa, A. A. (2007). Kaizen costing for lean manufacturing: a case study. International Journal of Production Research , 1751-1760.
- LISTA. (2012, november 5th). A three-step process for improving efficiency and productivity. Implementing 5S Workplace Organization , pp. 1-5.
- Bresko, M. (2005). The 5S Method of Improvement - Enhancing Safety, Productivity and Culture. ReliabilityDirect , 1-3.
- Worley, J. (2006). The role of communication and management support in a lean manufacturing implementation. Management Decision-Journal of Management History merged into Management Decision , 228-245.
- Gapp, R. (2008). Implementing 5S within a Japanese context: an integrated management system. Journal of Management History merged into Management Decision , 565 - 579.
- Ardith Ct., B. C. (2005). Workplace Color Coding Standards. visualworkplace , 1-5.
- Bayo‐Moriones, A. (2010). 5S use in manufacturing plants: contextual factors and impact on operating performance. International Journal of Quality & Reliability Management , 217 - 230.
- K. Ganapathy, Prof. V. Narayana, B. Subramanian – FIVE S, Quality Circle, Forum of India, Secunderabad.
- Motwani, J. (2003). A business process change framework for examining lean manufacturing: a case study. Industrial Management & Data Systems , 339-346.
- Shah, R. (2003). Lean manufacturing: context, practice bundles, and performance. Journal of Operations Management , 129-149.
- B. Modarressa, A. A. (2007). Kaizen costing for lean manufacturing: a case study. International Journal of Production Research , 1751-1760.
- LISTA. (2012, november 5th). A three-step process for improving efficiency and productivity. Implementing 5S Workplace Organization , pp. 1-5.
- Gapp, R. (2008). Implementing 5S within a Japanese context: an integrated management system. Journal of Management History merged into Management Decision , 565 - 579.
- Gapp, R. (2008). Implementing 5S within a Japanese context: an integrated management system. Journal of Management History merged into Management Decision , 565 - 579.
- Bresko, M. (2005). The 5S Method of Improvement - Enhancing Safety, Productivity and Culture. ReliabilityDirect , 1-3.
- Worley, J. (2006). The role of communication and management support in a lean manufacturing implementation. Management Decision-Journal of Management History merged into Management Decision , 228-245.
- Gapp, R. (2008). Implementing 5S within a Japanese context: an integrated management system. Journal of Management History merged into Management Decision , 565 - 579.
- Ardith Ct., B. C. (2005). Workplace Color Coding Standards. visualworkplace , 1-5.
- Bayo‐Moriones, A. (2010). 5S use in manufacturing plants: contextual factors and impact on operating performance. International Journal of Quality & Reliability Management , 217 - 230.
- K. Ganapathy, Prof. V. Narayana, B. Subramanian – FIVE S, Quality Circle, Forum of India, Secunderabad.
- Motwani, J. (2003). A business process change framework for examining lean manufacturing: a case study. Industrial Management & Data Systems , 339-346.
- Gapp, R. (2008). Implementing 5S within a Japanese context: an integrated management system. Journal of Management History merged into Management Decision , 565 - 579.
- Shah, R. (2003). Lean manufacturing: context, practice bundles, and performance. Journal of Operations Management , 129-149.
- Bresko, M. (2005). The 5S Method of Improvement - Enhancing Safety, Productivity and Culture. ReliabilityDirect , 1-3.
- Worley, J. (2006). The role of communication and management support in a lean manufacturing implementation. Management Decision-Journal of Management History merged into Management Decision , 228-245.
- B. Modarressa, A. A. (2007). Kaizen costing for lean manufacturing: a case study. International Journal of Production Research , 1751-1760.
- LISTA. (2012, november 5th). A three-step process for improving efficiency and productivity. Implementing 5S Workplace Organization , pp. 1-5.
- Shah, R. (2003). Lean manufacturing: context, practice bundles, and performance. Journal of Operations Management , 129-149.
- Ardith Ct., B. C. (2005). Workplace Color Coding Standards. visualworkplace , 1-5.
- Bayo‐Moriones, A. (2010). 5S use in manufacturing plants: contextual factors and impact on operating performance. International Journal of Quality & Reliability Management , 217 - 230.
- K. Ganapathy, Prof. V. Narayana, B. Subramanian – FIVE S, Quality Circle, Forum of India, Secunderabad.
- Motwani, J. (2003). A business process change framework for examining lean manufacturing: a case study. Industrial Management & Data Systems , 339-346.
- Shah, R. (2003). Lean manufacturing: context, practice bundles, and performance. Journal of Operations Management , 129-149.
- Gapp, R. (2008). Implementing 5S within a Japanese context: an integrated management system. Journal of Management History merged into Management Decision , 565 - 579.
- B. Modarressa, A. A. (2007). Kaizen costing for lean manufacturing: a case study. International Journal of Production Research , 1751-1760.
- LISTA. (2012, november 5th). A three-step process for improving efficiency and productivity. Implementing 5S Workplace Organization , pp. 1-5.
- Bresko, M. (2005). The 5S Method of Improvement - Enhancing Safety, Productivity and Culture. ReliabilityDirect , 1-3.
- Worley, J. (2006). The role of communication and management support in a lean manufacturing implementation. Management Decision-Journal of Management History merged into Management Decision , 228-245.
- Gapp, R. (2008). Implementing 5S within a Japanese context: an integrated management system. Journal of Management History merged into Management Decision , 565 - 579.
- Gapp, R. (2008). Implementing 5S within a Japanese context: an integrated management system. Journal of Management History merged into Management Decision , 565 - 579.
- Gapp, R. (2008). Implementing 5S within a Japanese context: an integrated management system. Journal of Management History merged into Management Decision , 565 - 579.
- Ardith Ct., B. C. (2005). Workplace Color Coding Standards. visualworkplace , 1-5.
- Bayo‐Moriones, A. (2010). 5S use in manufacturing plants: contextual factors and impact on operating performance. International Journal of Quality & Reliability Management , 217 - 230.
- K. Ganapathy, Prof. V. Narayana, B. Subramanian – FIVE S, Quality Circle, Forum of India, Secunderabad.
- Motwani, J. (2003). A business process change framework for examining lean manufacturing: a case study. Industrial Management & Data Systems , 339-346.
- Gapp, R. (2008). Implementing 5S within a Japanese context: an integrated management system. Journal of Management History merged into Management Decision , 565 - 579.
- Shah, R. (2003). Lean manufacturing: context, practice bundles, and performance. Journal of Operations Management , 129-149.
- B. Modarressa, A. A. (2007). Kaizen costing for lean manufacturing: a case study. International Journal of Production Research , 1751-1760.
- LISTA. (2012, november 5th). A three-step process for improving efficiency and productivity. Implementing 5S Workplace Organization , pp. 1-5.
- Bresko, M. (2005). The 5S Method of Improvement - Enhancing Safety, Productivity and Culture. ReliabilityDirect , 1-3.
- Worley, J. (2006). The role of communication and management support in a lean manufacturing implementation. Management Decision-Journal of Management History merged into Management Decision , 228-245.
- Gapp, R. (2008). Implementing 5S within a Japanese context: an integrated management system. Journal of Management History merged into Management Decision , 565 - 579.
- Ardith Ct., B. C. (2005). Workplace Color Coding Standards. visualworkplace , 1-5.
- Bayo‐Moriones, A. (2010). 5S use in manufacturing plants: contextual factors and impact on operating performance. International Journal of Quality & Reliability Management , 217 - 230.
- K. Ganapathy, Prof. V. Narayana, B. Subramanian – FIVE S, Quality Circle, Forum of India, Secunderabad.
- Motwani, J. (2003). A business process change framework for examining lean manufacturing: a case study. Industrial Management & Data Systems , 339-346.
- Gapp, R. (2008). Implementing 5S within a Japanese context: an integrated management system. Journal of Management History merged into Management Decision , 565 - 579.
- Ardith Ct., B. C. (2005). Workplace Color Coding Standards. visualworkplace , 1-5.
- Ardith Ct., B. C. (2005). Workplace Color Coding Standards. visualworkplace , 1-5.
- Bayo‐Moriones, A. (2010). 5S use in manufacturing plants: contextual factors and impact on operating performance. International Journal of Quality & Reliability Management , 217 - 230.
- K. Ganapathy, Prof. V. Narayana, B. Subramanian – FIVE S, Quality Circle, Forum of India, Secunderabad.
- Motwani, J. (2003). A business process change framework for examining lean manufacturing: a case study. Industrial Management & Data Systems , 339-346.
- B. Modarressa, A. A. (2007). Kaizen costing for lean manufacturing: a case study. International Journal of Production Research , 1751-1760.
- LISTA. (2012, november 5th). A three-step process for improving efficiency and productivity. Implementing 5S Workplace Organization , pp. 1-5.
- Bresko, M. (2005). The 5S Method of Improvement - Enhancing Safety, Productivity and Culture. ReliabilityDirect , 1-3.
- Worley, J. (2006). The role of communication and management support in a lean manufacturing implementation. Management Decision-Journal of Management History merged into Management Decision , 228-245.
- Bresko, M. (2005). The 5S Method of Improvement - Enhancing Safety, Productivity and Culture. ReliabilityDirect , 1-3.
- Bayo‐Moriones, A. (2010). 5S use in manufacturing plants: contextual factors and impact on operating performance. International Journal of Quality & Reliability Management , 217 - 230.
- K. Ganapathy, Prof. V. Narayana, B. Subramanian – FIVE S, Quality Circle, Forum of India, Secunderabad.
- Motwani, J. (2003). A business process change framework for examining lean manufacturing: a case study. Industrial Management & Data Systems , 339-346.
- Worley, J. (2006). The role of communication and management support in a lean manufacturing implementation. Management Decision-Journal of Management History merged into Management Decision , 228-245.
- Gapp, R. (2008). Implementing 5S within a Japanese context: an integrated management system. Journal of Management History merged into Management Decision , 565 - 579.
- Shah, R. (2003). Lean manufacturing: context, practice bundles, and performance. Journal of Operations Management , 129-149.
- Gapp, R. (2008). Implementing 5S within a Japanese context: an integrated management system. Journal of Management History merged into Management Decision , 565 - 579.
- Gapp, R. (2008). Implementing 5S within a Japanese context: an integrated management system. Journal of Management History merged into Management Decision , 565 - 579.
- Ardith Ct., B. C. (2005). Workplace Color Coding Standards. visualworkplace , 1-5.
- Bayo‐Moriones, A. (2010). 5S use in manufacturing plants: contextual factors and impact on operating performance. International Journal of Quality & Reliability Management , 217 - 230.
- K. Ganapathy, Prof. V. Narayana, B. Subramanian – FIVE S, Quality Circle, Forum of India, Secunderabad.
- Motwani, J. (2003). A business process change framework for examining lean manufacturing: a case study. Industrial Management & Data Systems , 339-346.
- Shah, R. (2003). Lean manufacturing: context, practice bundles, and performance. Journal of Operations Management , 129-149.
- Gapp, R. (2008). Implementing 5S within a Japanese context: an integrated management system. Journal of Management History merged into Management Decision , 565 - 579.
- Ardith Ct., B. C. (2005). Workplace Color Coding Standards. visualworkplace , 1-5.
- Bayo‐Moriones, A. (2010). 5S use in manufacturing plants: contextual factors and impact on operating performance. International Journal of Quality & Reliability Management , 217 - 230.
- K. Ganapathy, Prof. V. Narayana, B. Subramanian – FIVE S, Quality Circle, Forum of India, Secunderabad.
- Motwani, J. (2003). A business process change framework for examining lean manufacturing: a case study. Industrial Management & Data Systems , 339-346.
- Worley, J. (2006). The role of communication and management support in a lean manufacturing implementation. Management Decision-Journal of Management History merged into Management Decision , 228-245.
- B. Modarressa, A. A. (2007). Kaizen costing for lean manufacturing: a case study. International Journal of Production Research , 1751-1760.
- LISTA. (2012, november 5th). A three-step process for improving efficiency and productivity. Implementing 5S Workplace Organization , pp. 1-5.
- Bresko, M. (2005). The 5S Method of Improvement - Enhancing Safety, Productivity and Culture. ReliabilityDirect , 1-3.
- Worley, J. (2006). The role of communication and management support in a lean manufacturing implementation. Management Decision-Journal of Management History merged into Management Decision , 228-245.
- Shah, R. (2003). Lean manufacturing: context, practice bundles, and performance. Journal of Operations Management , 129-149.
- B. Modarressa, A. A. (2007). Kaizen costing for lean manufacturing: a case study. International Journal of Production Research , 1751-1760.
- LISTA. (2012, november 5th). A three-step process for improving efficiency and productivity. Implementing 5S Workplace Organization , pp. 1-5.
- Shah, R. (2003). Lean manufacturing: context, practice bundles, and performance. Journal of Operations Management , 129-149.
- Ardith Ct., B. C. (2005). Workplace Color Coding Standards. visualworkplace , 1-5.
- Bayo‐Moriones, A. (2010). 5S use in manufacturing plants: contextual factors and impact on operating performance. International Journal of Quality & Reliability Management , 217 - 230.
- K. Ganapathy, Prof. V. Narayana, B. Subramanian – FIVE S, Quality Circle, Forum of India, Secunderabad.
- Motwani, J. (2003). A business process change framework for examining lean manufacturing: a case study. Industrial Management & Data Systems , 339-346.
- B. Modarressa, A. A. (2007). Kaizen costing for lean manufacturing: a case study. International Journal of Production Research , 1751-1760.
- LISTA. (2012, november 5th). A three-step process for improving efficiency and productivity. Implementing 5S Workplace Organization , pp. 1-5.
- Bresko, M. (2005). The 5S Method of Improvement - Enhancing Safety, Productivity and Culture. ReliabilityDirect , 1-3.
- Ardith Ct., B. C. (2005). Workplace Color Coding Standards. visualworkplace , 1-5.
- Bayo‐Moriones, A. (2010). 5S use in manufacturing plants: contextual factors and impact on operating performance. International Journal of Quality & Reliability Management , 217 - 230.
- K. Ganapathy, Prof. V. Narayana, B. Subramanian – FIVE S, Quality Circle, Forum of India, Secunderabad.
- Motwani, J. (2003). A business process change framework for examining lean manufacturing: a case study. Industrial Management & Data Systems , 339-346.
- Ardith Ct., B. C. (2005). Workplace Color Coding Standards. visualworkplace , 1-5.
- Bayo‐Moriones, A. (2010). 5S use in manufacturing plants: contextual factors and impact on operating performance. International Journal of Quality & Reliability Management , 217 - 230.
- K. Ganapathy, Prof. V. Narayana, B. Subramanian – FIVE S, Quality Circle, Forum of India, Secunderabad.
- Motwani, J. (2003). A business process change framework for examining lean manufacturing: a case study. Industrial Management & Data Systems , 339-346.
- B. Modarressa, A. A. (2007). Kaizen costing for lean manufacturing: a case study. International Journal of Production Research , 1751-1760.
- LISTA. (2012, november 5th). A three-step process for improving efficiency and productivity. Implementing 5S Workplace Organization , pp. 1-5.
- Bresko, M. (2005). The 5S Method of Improvement - Enhancing Safety, Productivity and Culture. ReliabilityDirect , 1-3.
- Worley, J. (2006). The role of communication and management support in a lean manufacturing implementation. Management Decision-Journal of Management History merged into Management Decision , 228-245.
- Bresko, M. (2005). The 5S Method of Improvement - Enhancing Safety, Productivity and Culture. ReliabilityDirect , 1-3.
- Worley, J. (2006). The role of communication and management support in a lean manufacturing implementation. Management Decision-Journal of Management History merged into Management Decision , 228-245.
- Gapp, R. (2008). Implementing 5S within a Japanese context: an integrated management system. Journal of Management History merged into Management Decision , 565 - 579.
- Shah, R. (2003). Lean manufacturing: context, practice bundles, and performance. Journal of Operations Management , 129-149.
- Ardith Ct., B. C. (2005). Workplace Color Coding Standards. visualworkplace , 1-5.
- Bayo‐Moriones, A. (2010). 5S use in manufacturing plants: contextual factors and impact on operating performance. International Journal of Quality & Reliability Management , 217 - 230.
- K. Ganapathy, Prof. V. Narayana, B. Subramanian – FIVE S, Quality Circle, Forum of India, Secunderabad.
- Motwani, J. (2003). A business process change framework for examining lean manufacturing: a case study. Industrial Management & Data Systems , 339-346.
- Shah, R. (2003). Lean manufacturing: context, practice bundles, and performance. Journal of Operations Management , 129-149.
- Bresko, M. (2005). The 5S Method of Improvement - Enhancing Safety, Productivity and Culture. ReliabilityDirect , 1-3.
- Worley, J. (2006). The role of communication and management support in a lean manufacturing implementation. Management Decision-Journal of Management History merged into Management Decision , 228-245.
- B. Modarressa, A. A. (2007). Kaizen costing for lean manufacturing: a case study. International Journal of Production Research , 1751-1760.
- LISTA. (2012, november 5th). A three-step process for improving efficiency and productivity. Implementing 5S Workplace Organization , pp. 1-5.
|
Article Post Production
No data exists for the row/column.
|